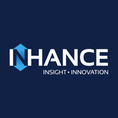
INHANCE WMS
Receiving
Guided by inbound instructions, our system efficiently records product specifics and prepares stock for put-away using uniquely assigned pallets, streamlining warehouse operations. This process is supported by robust features, including the ability to handle multiple deliveries against an original order, manage both planned and unplanned returns, and receive stock into designated locations or bays. Key details such as vehicle information, delivery notes, and related documentation are meticulously recorded, while restricted over-receipt rules ensure accuracy. Additional functionalities include batch registration with expiry dates, sample extraction for products requiring it, and comprehensive labelling for items, cartons, and pallets. The system also facilitates the recording of damages, importing of documentation, and receiving by any defined pack unit of measure, such as unit, case, or pallet. Once receiving is completed, GRVs can be emailed automatically, and put-away jobs—whether for single SKU or mixed SKU loads—are seamlessly created to optimise workflow.
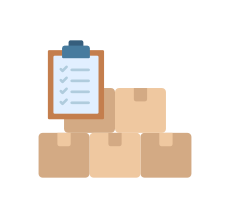
Put-away
Our system effectively manages and oversees the entire put-away process, ensuring structured and efficient operations. Put-away assignments and pallets are staged systematically, with each pallet assigned a unique number plate to initiate and guide the process. The system features guided slotting, which can be overridden by operators if necessary. It assesses whether received stock should be placed in pick bins or bulk storage, based on predefined minimum and maximum quantities for pick bins and batch-related business rules. Real-time visibility is provided for the duration stock remains staged before being put away, with urgent stock prioritised accordingly. Cross-dock stock is directed to a designated staging area for seamless handling. The process is powered by RF scanning, enabling real-time updates and system-directed storage adjustments in case of errors, ensuring accuracy and efficiency at every step.
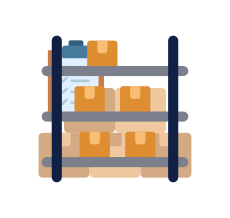
Inventory Management
Inventory management involves comprehensive tasks such as stock control, location management, and efficient task allocation tailored to operator priorities. Key features include the allocation of products to specific store locations, system-directed put-away, and assigning put-away tasks to designated user groups. The process supports two-stage put-away from receiving and includes pick bin setup with regular health checks. Movements are managed through RF scanners, and system-generated replenishments from bulk to pick bins are triggered based on predefined minimum and maximum quantities. Task allocation is role-based, linking operators to specific areas or zones, with tasks assigned accordingly. Additionally, task-type priorities can be set for individual operators rather than entire operator groups, ensuring flexibility in resource allocation based on specific requirements.
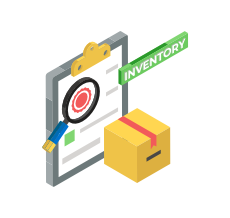
Planning
We support diverse planning strategies, releasing tasks tailored to your business type and operational needs. Our system enables the planning of outbound documents based on priorities, splitting pick jobs across different areas within the warehouse, and managing outbound order delivery dates effectively. It ensures optimal floor workload management by balancing the number of orders released for picking and links multiple outbound orders to a single shipment for enhanced picking efficiency through bulk picks. Stock is allocated to designated pick locations, with batches assigned based on the FEFO (First Expiry, First Out) principle. Dashboard views provide real-time visibility of workloads, ensuring tasks are completed within specified cut-offs. Additionally, the system automatically builds pick jobs based on defined parameters, streamlining operations and improving overall efficiency.
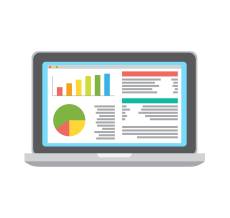
Picking
Our system streamlines the picking process by efficiently organising pick instructions and prioritising tasks for pickers, either from the queue or through specific job allocations. Key features include the ability to perform full picks from bulk storage or partial picks from the pick face, along with comprehensive pick job management such as status tracking, pausing, and reissuing short picks before completing the process. The system also supports exception stock counts and provides automated redirection to alternative locations in the event of a short pick. Batch numbers are confirmed during the pick job, ensuring accuracy, while pick jobs are allocated to the appropriate user group for efficient execution. Additionally, outbound shipments are consolidated into selected dispatch locations, enhancing organisation and operational efficiency.
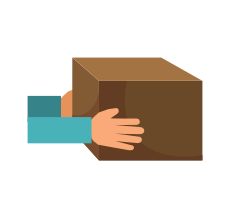
Checking
Our system offers flexible checking options, accommodating both scanner-based and paper-based methods to suit your warehouse operation needs. Supported features include the ability to customise the checking process based on specific requirements, such as checking by product, SKU (e.g., quantities of 1 litre, 5 litres, or 20 litres), or customer. The system also supports bulk picking across customers, allowing items to be repacked and checked by customer or into different boxes. Checking can be tailored to include or exclude certain product categories as needed. Once an entire order has been checked—potentially involving multiple pick jobs—the system can trigger the update of the outbound order on the ERP and initiate invoicing. Dashboards provide real-time progress views of all jobs in checking, including those requiring authorisation, ensuring complete visibility and control throughout the process.
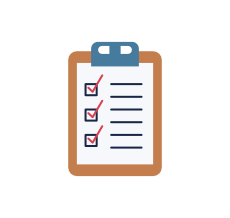
Dispatch
Our system delivers a streamlined and accountable dispatch process, ensuring efficiency at every stage. Stock is scanned and confirmed into dispatch and onto the vehicle, with seamless handovers between checking and dispatch. Real-time dashboard views provide visibility into all routes and the status of orders staged for dispatch. The system meticulously builds loads and trips, preventing trip closure until all packages are scanned to ensure no stock is left behind. Dispatch documentation is only generated once the vehicle is fully loaded and the trip is closed, guaranteeing a well-organised, accurate, and error-free dispatch operation.
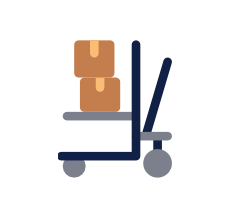
Debriefing
Upon returning to the warehouse, drivers are required to submit any remaining vehicle stock and provide signed proof-of-delivery (POD) documents, ensuring complete accountability and transparency. The system supports the handling of PODs, receiving planned customer returns, and managing undelivered stock by placing the order back into dispatch status. This includes cases of non-delivery or rejected deliveries, which can be rescheduled for re-delivery if necessary. For unplanned returns, the system allows the creation of credit notes within the WMS, recording stock against appropriate reason codes such as damages in transit, lost in transit, or delivery to the incorrect customer. This structured approach ensures accurate tracking and management of returned stock.
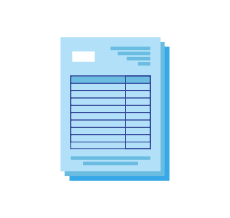